SERVICE TYPE ONE | SERVICE TWO
Waffle Deck
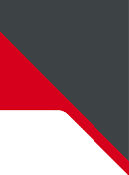
CLIENT
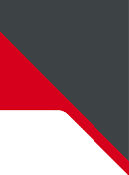
PROJECT ACHIEVEMENTS
- Project delivered ahead of schedule
- 219,002 Incident free hours recorded
- 166,400 Displaced site-based hours
The client has very precise and exacting standards with respect to the material, product finish and critical dimensions of each of the waffle formers. Each waffle dome for example had 25 individual moving parts which meant multiple subset assemblies prior to product modularisation.
To enable the fabrication process multiple dies first had to manufactured to produce 14 varying pressed panel types. Materials, components and products had to be sourced from 3 different continents and where possible certain items had to be bespoke manufactured to maintain fabrication and installation deadlines.
The total project tonnage was 5,680 tonnes, consisting of 29,760 individual formers combined into 2,352 modules.
To ensure we met project milestones the challenge was to modularise the process which would in turn,
Reduce On Site Risk
Ensure Project Quality
Speed up Site Installation
Modularisation is a great process but needs careful consideration when choosing it as part of your project delivery strategy. We were confident after considerable review with our preconstruction delivery team that we could modularise this project successfully.
Because we chouse the modular route for delivery it meant that we could condense 29,760 individual formers into 2,352 modules with 12 individual domes in each module. The size of which were 2.4m x 6.7m with a depth ranging between 0.7 and 1.2m deep.
To be able to deliver modularisation we then needed to design, fabricate and certify a one-off bespoke specialist lifting apparatus that could load, offload and place in position each of the modules.