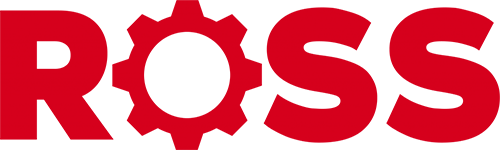
POLYMER
Our commitment to quality is unwavering, and we proudly hold certifications to ISO 9001 and 13485 standards. With over four decades of hands-on experience in injection moulding technologies and polymer material development, our technical prowess is second to none.
Equipped with both horizontal and vertical moulding capabilities, extending up to 400 tonnes, and a full suite of testing and quality control equipment, all housed within a state-of-the-art manufacturing facility, we are the premier partner to oversee and execute all your technical projects.
We specialise in ushering in new product introductions and handling small to high-volume manufacturing for the medical, life science, and semiconductor sectors. At Ross Polymer Services, our primary objective is to consistently achieve the highest level of quality in everything we do.
CAPABILITIES
Our capabilities in injection moulding are extensive, covering a range from 50 to 400-tonne machines, along with a specialized 50-tonne vertical moulding machine capable of various over-moulding projects within the medical, electronics, and semiconductor sectors.
To ensure consistent quality, we employ rigorous quality checks and implement statistical process control techniques, ensuring process stability and the highest part quality for each and every shot. This dedication to excellence is upheld in a lean production moulding environment.
We employ insert change tooling technology, facilitating swift tool changes and reducing downtime. This technology is particularly valuable in the early stages of tool design and manufacturing, expediting the development cycle and fast-tracking the product development process, ultimately expediting our customers’ time-to-market.
ROSS Polymer team is your partner throughout the injection moulding project, offering support from initial product design and prototyping to material selection and the creation of multi-cavity production tooling. Our goal is to help our clients bring their products to market as efficiently as possible. Our team of experts is with you every step of the way, from design and first-off samples to validation runs and the implementation of any necessary sub-assembly technologies, providing a comprehensive turnkey solution.
Additionally, our value-added capabilities encompass:
- Product Design and Design for Manufacture (DFM
- Ultrasonic Welding
- Pad Printing
- Heat Seal Packaging
- Adhesive Bonding
Take a tour of our polymer facility
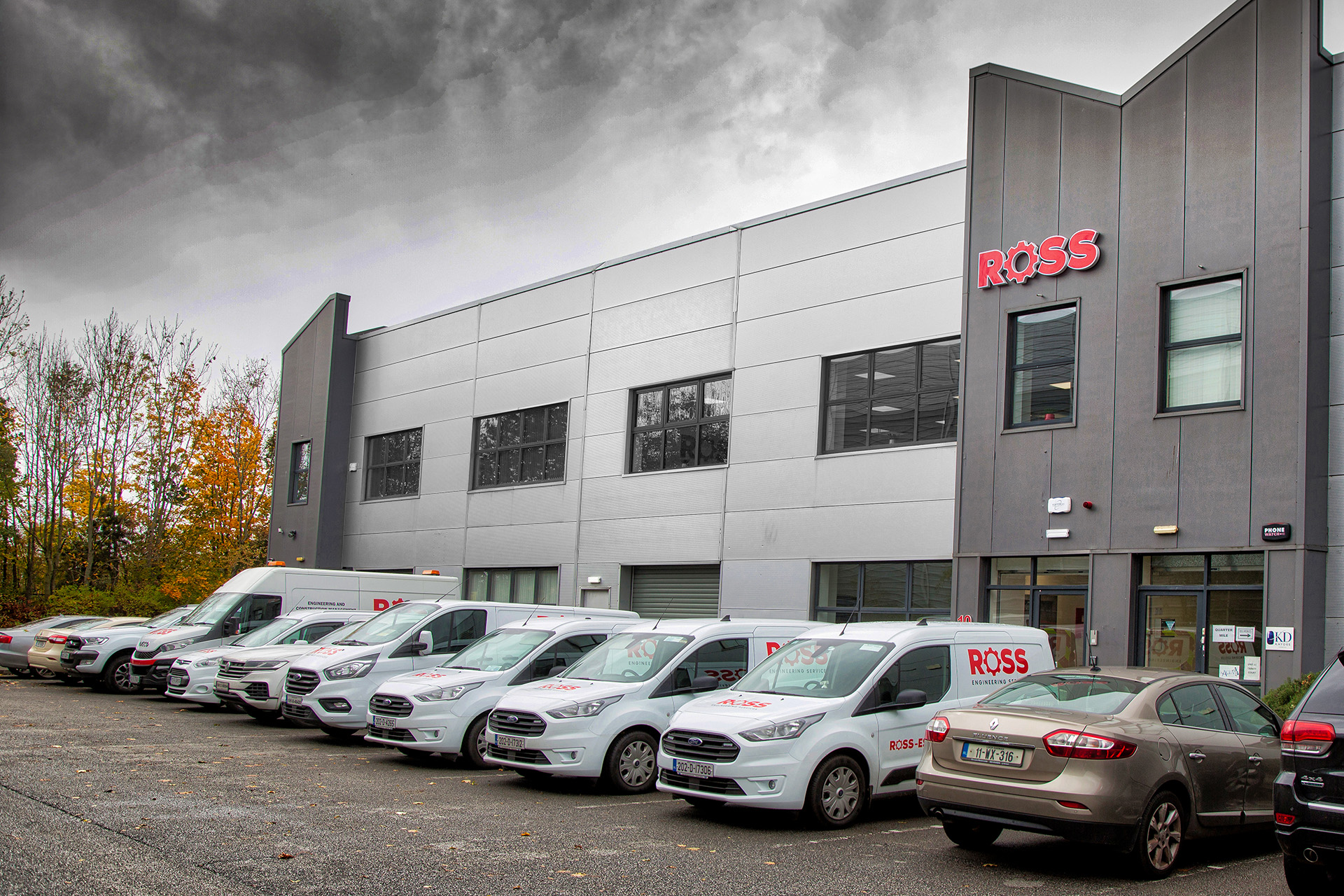
Project Management
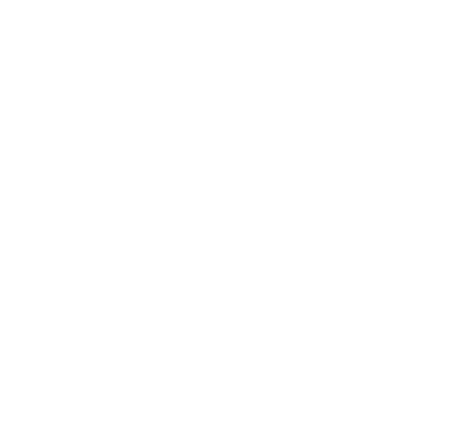
We support clients through every stage of their injection moulding projects, from initial design and prototyping to material selection, multi-cavity production tooling, and manufacturing. Our goal is to expedite the product t -market process efficiently.
Our experts are available throughout the entire process, offering guidance on design, first-off samples, validation runs, and the implementation of any necessary sub-assembly technologies, providing a comprehensive conception-to-completion service.
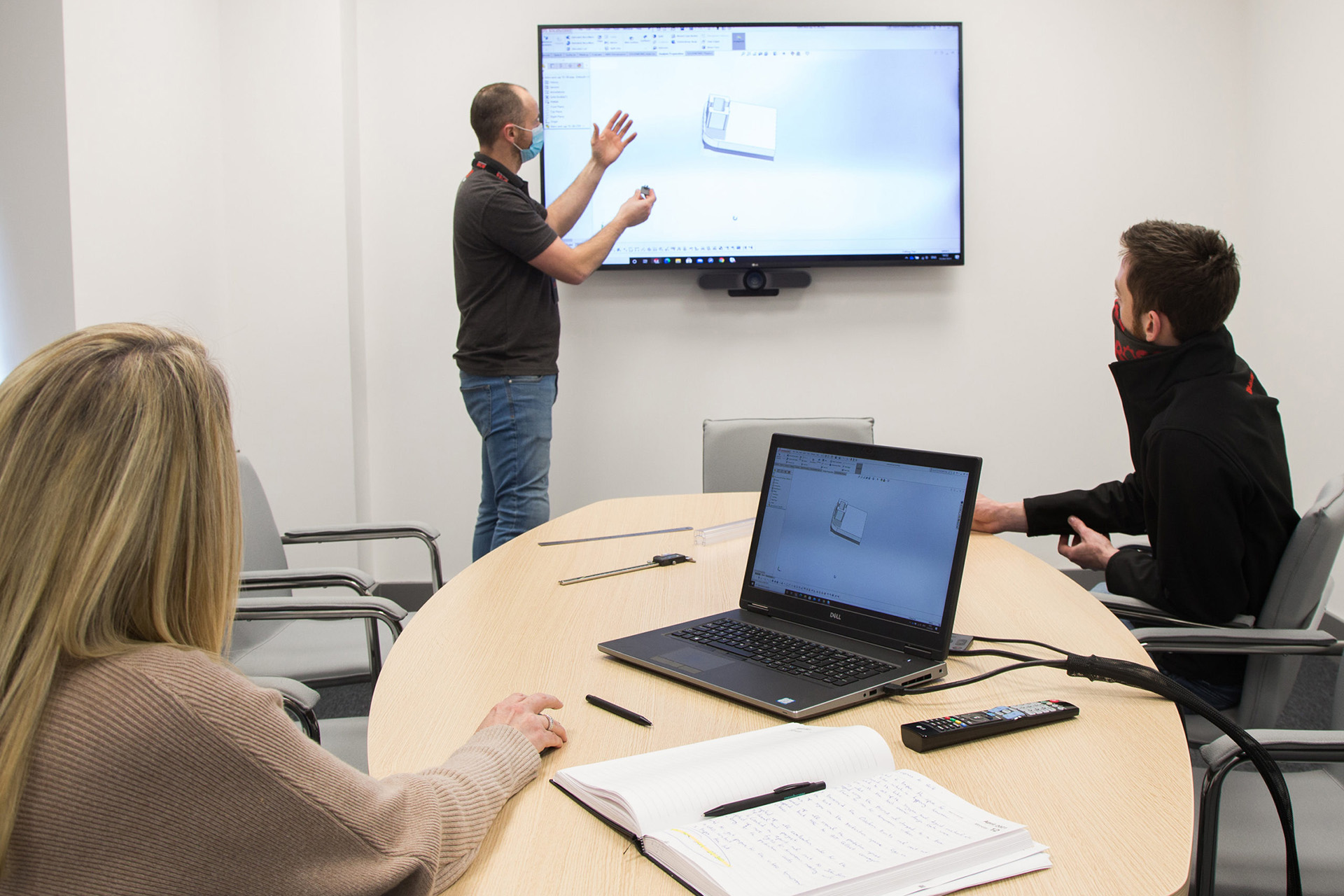
Design
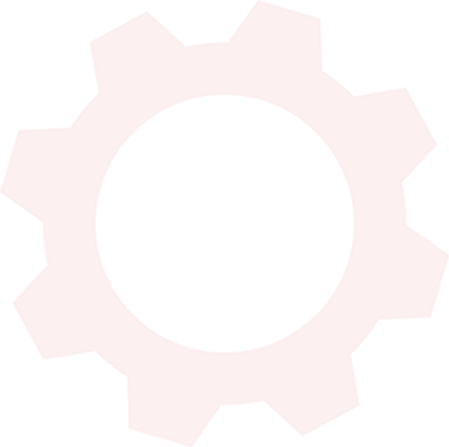
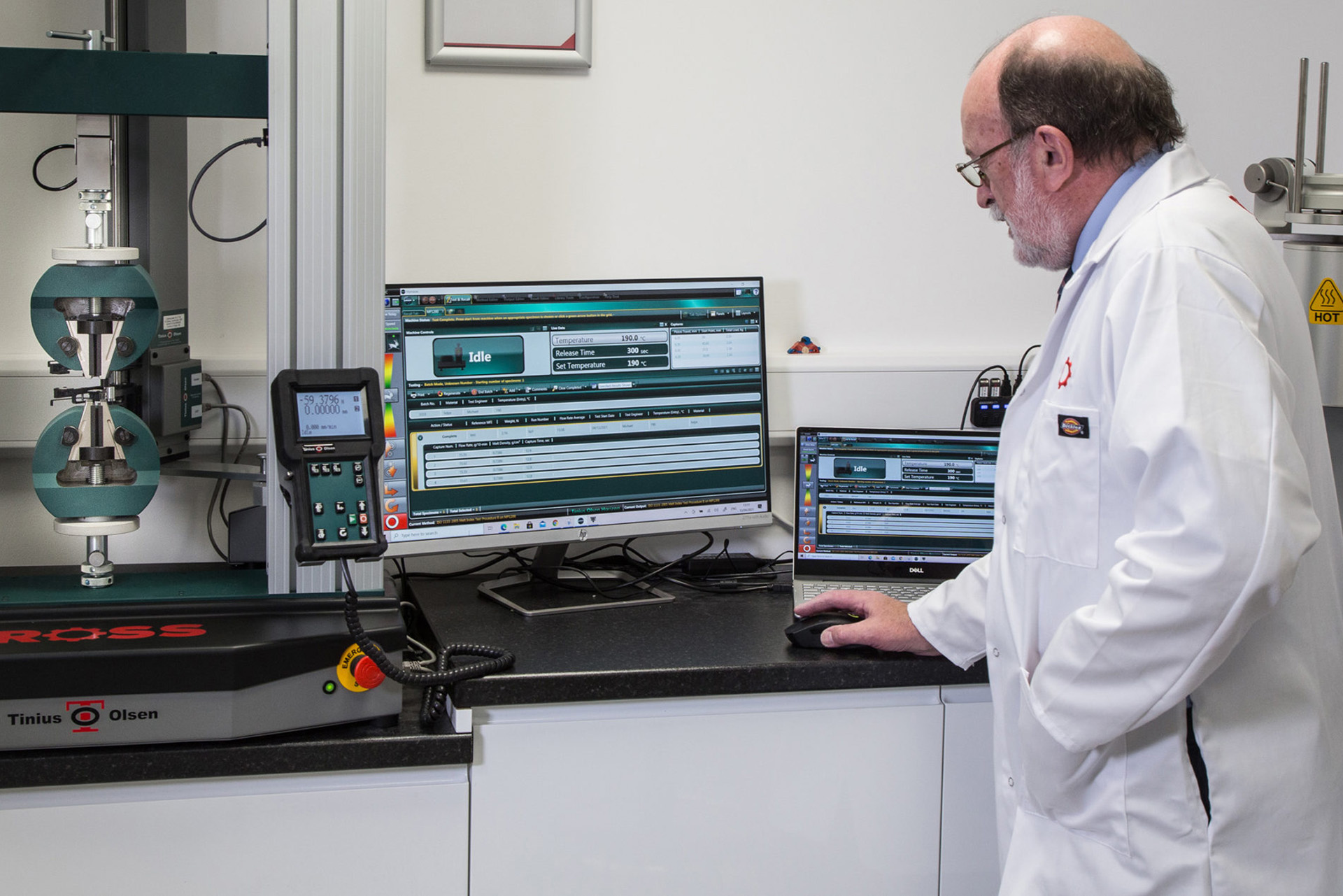
Mould Flow Analysis
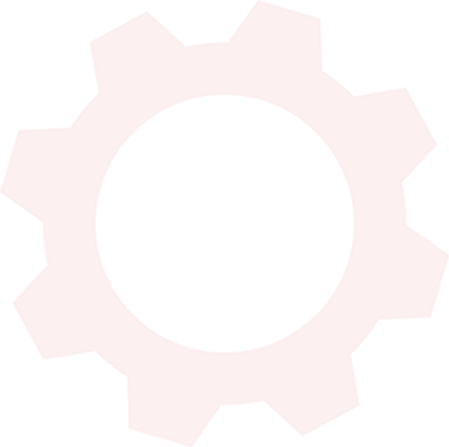
This service gives the customer the responsive action needed to design and manufacture the most efficient and optimised tool possible. All results can be presented on a one-to-one basis or on a remote platform to give the client the best possible understanding of the simulations.
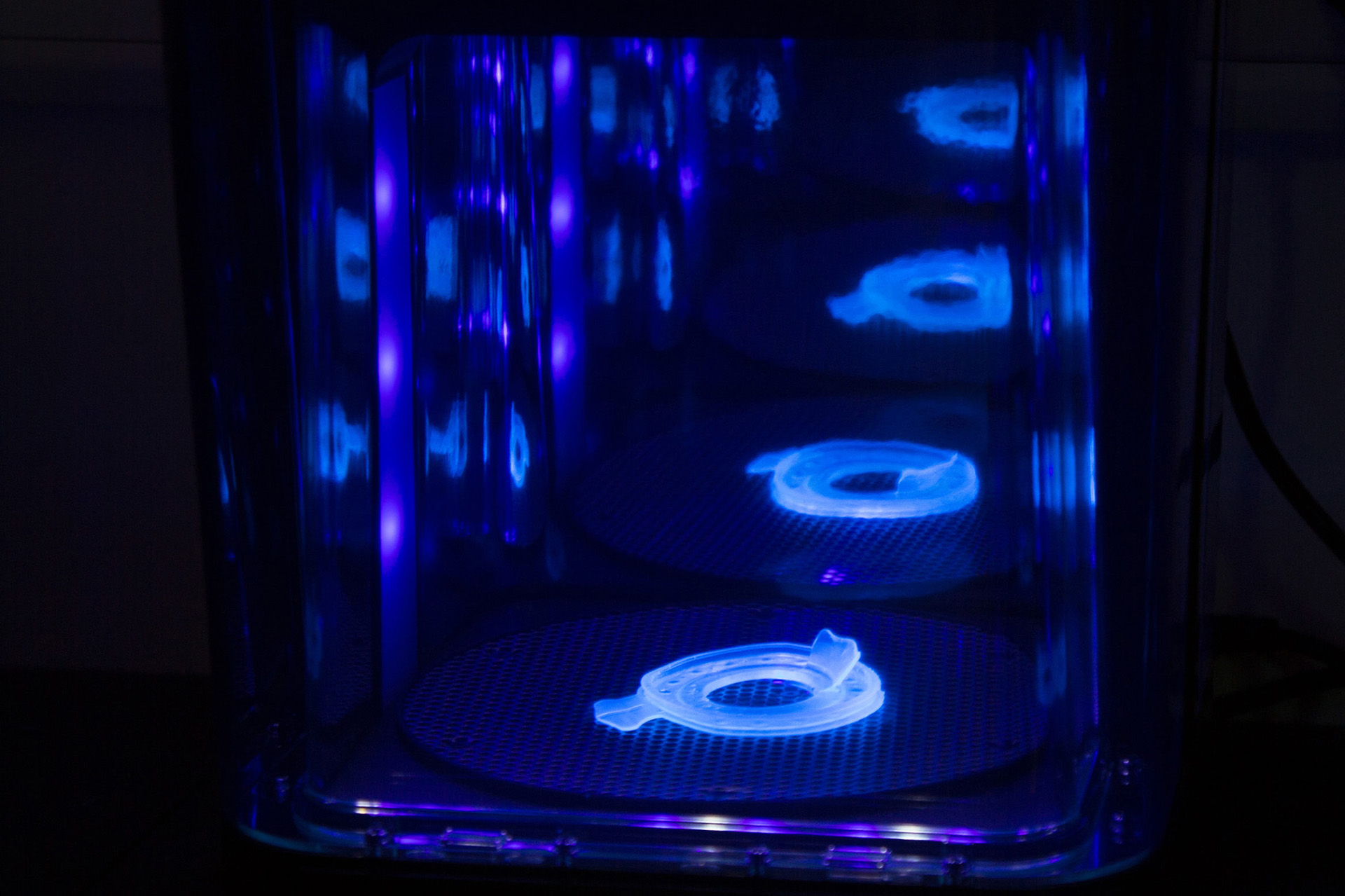
3D Printing and Protyping
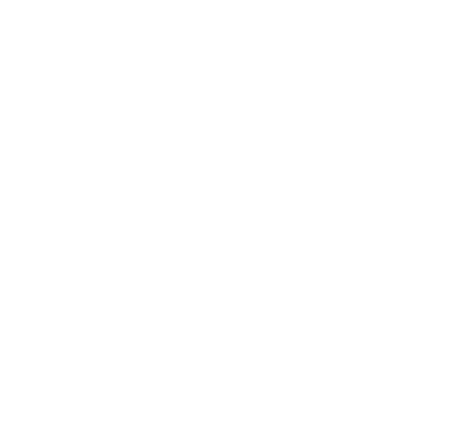
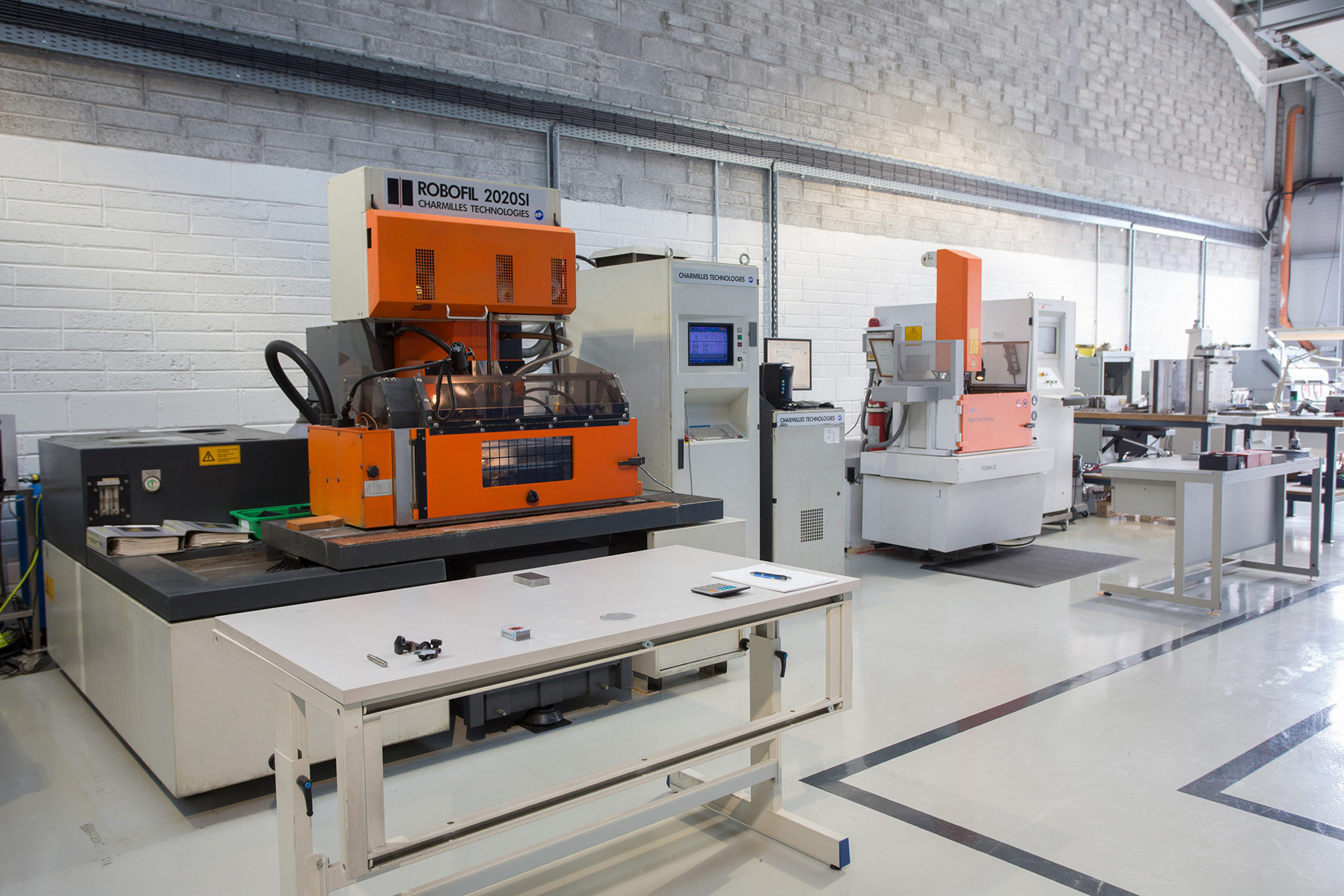
Tool Manufacture
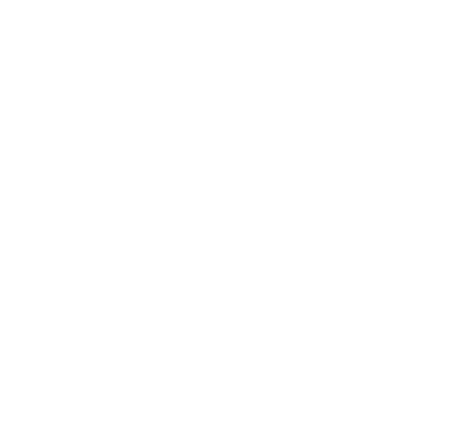
We have worked with all types of tool designs and configurations from aluminium and P20 tools for prototyping to fully hardened multi cavitation production tooling suitable for the manufacture of a range of materials from standard Polyolefins to high temperature heavily filled thermoplastic composites. Whatever the project requirements we are confident we can produce a tool in line with your projects specifications and commercial needs.
At ROSS the tooling service doesn’t stop at fabrication. All tools enter into our comprehensive maintenance programme to ensure that all tools are fully serviced and maintained to achieve optimum longevity and part quality.
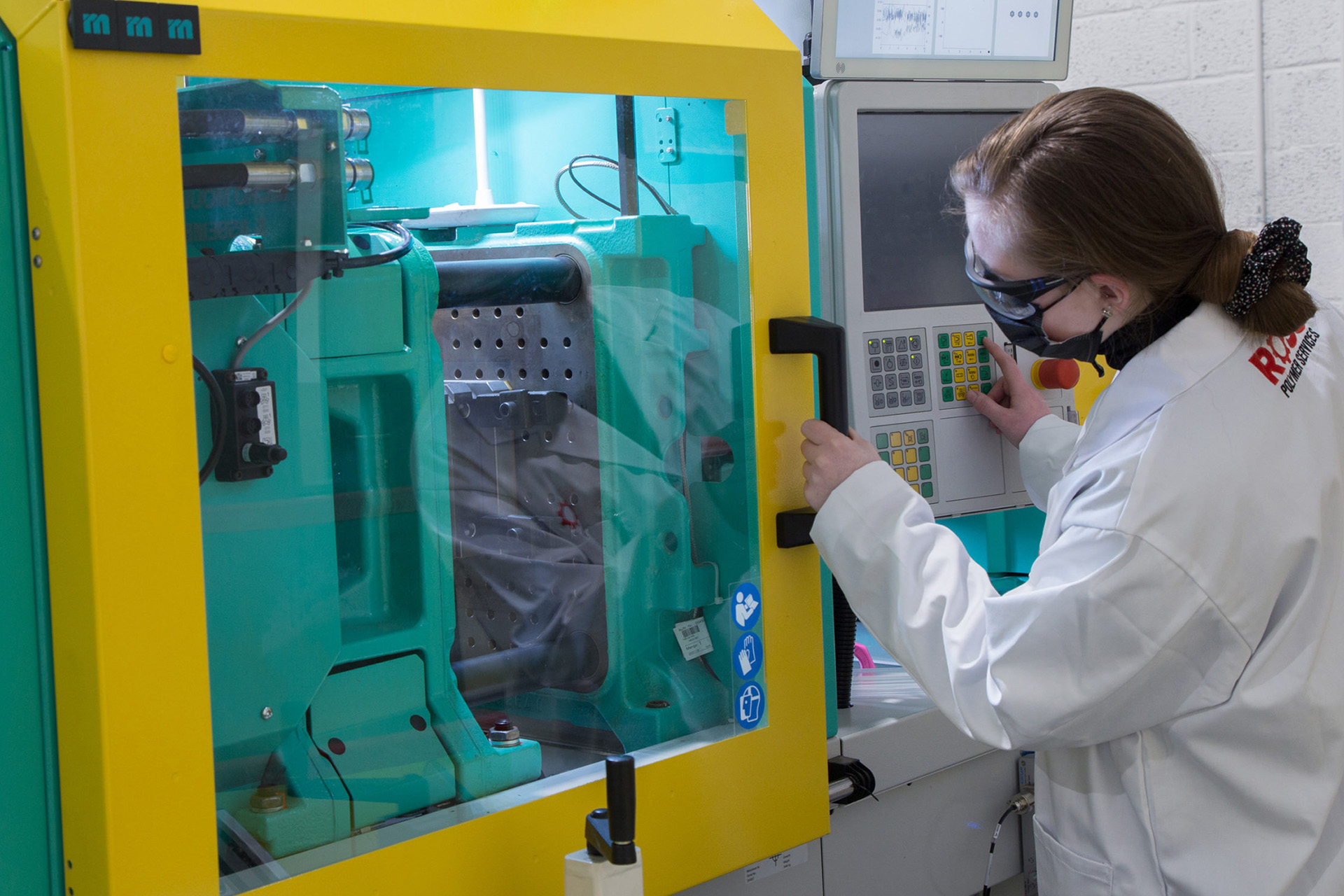
Contract Manufacture
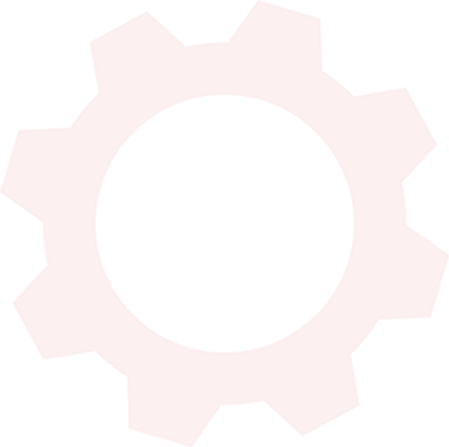
Our extensive range of state-of-the-art injection moulding machines mean that most custom moulding requirements can be met. We have the capability to produce injection mouldings from 0.01g to 2.5kg in shot weight whilst also having the capability to process high temperature materials in a controlled fashion. We offer the opportunity to clients to access a range of state of the art injection moulding equipment for pilot production runs or validation studies.
All incoming materials are evaluated in terms of rheological and mechanical properties as well as its moisture content before and after drying in our state of the art testing labs. All elements of the process are monitored and recorded on our industry 4.0 designed data acquisition platform allowing the customer to monitor all aspects of their process in real time.
Our in-mould pressure monitoring system allows us to implement the highest level of part quality from shot to shot insuring a zero part defect approach whilst also giving the customer the opportunity to implement a full part to part traceability system which can offer all processing perimeters specific to any individual part.
This really is a cradle to grave service offering our clients the option of a single source service provider to assist with the delivery of their projects.
Remember “Your Challenge, Our Solution”.